Varnishing the Brightwork
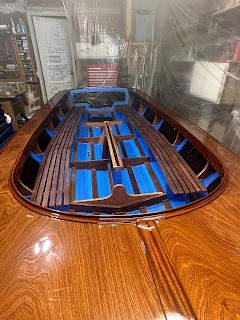
There is quite a bit of exposed Sapele woodwork in the cockpit, including the frames, centerboard trunk, seats, and floorboards, that also needs to be varnished for UV protection. I bought a gallon of TotalBoat Gleam 2.0 High Gloss, a one part varnish. Three coats of the Gleam can be applied in one day without sanding, which is good because the exposed wood will need needs 4-6 coats of varnish for UV protection. To make applying the varnish easier and neater, I used painters tape and plastic to protect all the painted surfaces so I don’t have to spend a lot of time cutting in and risk inevitably getting varnish on the white painted hull on every coat. It took a long time (probably over 8 hours) to tape off everything, but it saved a lot of time overall because it made applying each of the 7 coats so much faster. The photo below is 6 coats of varnish on the interior framing (no varnish on the seats yet). I’m going to sand and apply one more coat for 7 total coats. I varnished the floor